高精度五軸雷射進動掃描技術如何提升微加工能力
五軸掃描頭是一種快速且靈活的解決方案,能夠精準加工各種孔洞、輪廓槽及其他幾何形狀,並確保其橫截面符合設計要求。透過適當的系統配置,整個微加工過程——從雷射控制、掃描頭運動到工件定位——都能被精確掌控,使加工範圍涵蓋從宏觀尺寸到次微米級的高精度零件。
本文將介紹五軸雷射進動掃描頭的工作原理,以 Aerotech AGV5D 為例,結合精密線性運動軸與控制系統,說明其如何運作;此外,將深入解析該系統如何透過 G-code(RS-274)程式設計,讓 CAM(電腦輔助製造) 軟體與內建運動功能協同運作,以達成微米級的高精度鑽孔與銑削加工。
五軸雷射運動系統:工作原理
全面理解五軸雷射運動系統在微鑽孔與銑削應用中的優勢(如圖 1 所示),以及其在這類加工過程中的精度量化方式,需要深入了解該系統的工作原理以及其程式設計方式。
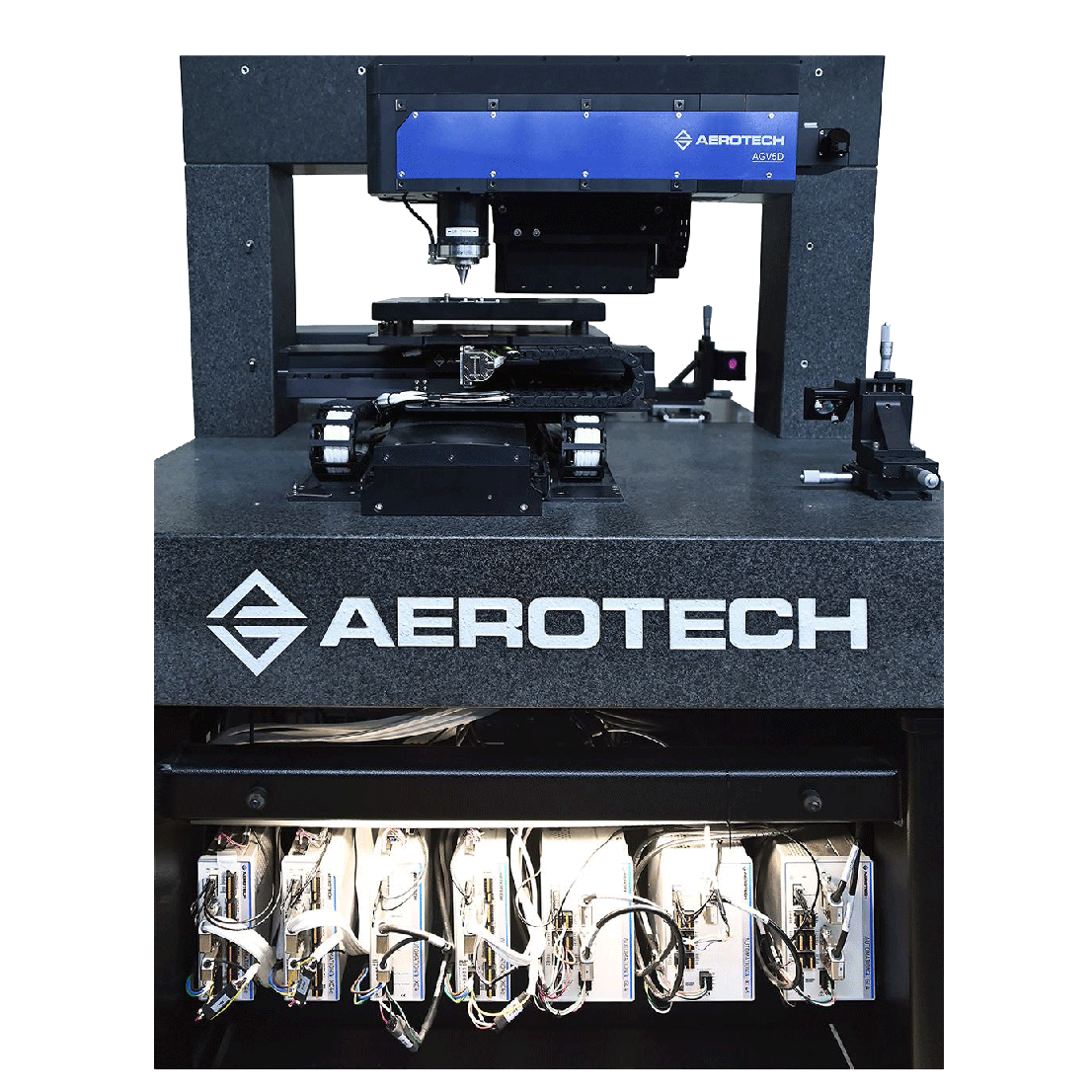
圖 1. 本文參考的五軸雷射運動系統,包含 AGV5D 五軸進動掃描頭
本文介紹的範例系統使用 Aerotech AGV5D 五軸進動(Precession)掃描頭,透過 五個自由度(DOF) 精確控制雷射光束的移動,如圖 2 所示:
- X 與 Y 軸:調整雷射光點在加工區域內的位置,無論 Z 軸高度 為何(2 個自由度)。
- Z 軸:控制焦點深度,使雷射可聚焦在不同高度(1 個自由度)。
- A 軸:調整光束的傾斜角度,改變切削或鑽孔時的錐度(1 個自由度)。
- C 軸:旋轉光束方向,確保加工時能從不同角度進行切削(1 個自由度)。
AGV5D 掃描頭的最大加工範圍為 2 mm 直徑的圓形區域(X、Y 方向),高度範圍則為 2 mm(Z 方向);光束的 傾斜角度(A 軸) 可達 ±9°,而 旋轉角度(C 軸) 則可 360° 無限旋轉,確保加工時的靈活度與精度。
類似於五軸 CNC 加工中心的運作方式
AGV5D 使用符合 RS-274 標準的 G-code 指令來控制雷射光束,使其能沿著 2D 或 3D 路徑(直線與圓弧) 運動,雷射光束從 掃描頭底部的噴嘴 發射,因此實際的加工區域位於噴嘴的最下方,所有運動軌跡都作用於 AGV5D 的 X-Y-Z-A-C 軸,確保雷射光點能夠準確地對焦並執行精密加工。
除了五個自由度(DOF)的光束控制外,該系統還支援額外的軸向運動,並可由 相同的控制器與 G-code 指令 同步控制;外部 X、Y 和 Z 軸 負責移動工件,使其在掃描頭下方移動,以擴大加工視野,並與光束運動進行同步協調;由於 Aerotech Automation1 軟體型機器控制器(iSMC, Integrated System Motion Controller) 負責管理整個系統,因此 G-code 軌跡 可與 Aeroscript 程式指令協同運作,以提供更靈活的加工控制。
在此範例系統中,AGV5D 的 X-Y-Z-A-C 軸 由 200 kHz 驅動器 控制雷射光束定位,而負責移動基板與掃描頭的 外部 X-Y-Z 軸 則由 20 kHz 伺服驅動 控制,所有驅動器都連接在同一網路,並由 Automation1 進行同步控制;因此,在同時控制 八個軸 的軌跡時,所有驅動器都能夠透過同一控制器即時運行;這種架構讓 AGV5D 能夠在 單一控制器架構 下同時管理 伺服馬達與雷射掃描頭的運動,提升系統的靈活性,並最佳化零件的加工效率。
靈活的程式設計功能
在這類應用中,系統提供了多種程式設計工具,以提升加工靈活性,使用者可透過 標準 CAM(電腦輔助製造)軟體 產生 G-code,但前提是該軟體具備適用於該系統運動學的 後處理器(Post-Processor);這些 G-code 指令可直接用於 銑削模式(Milling Mode),讓使用者能夠 定義切削直徑、加工路徑與速度,確保達到所需的切割品質與精度;圖 3 是一個利用 銑削模式 進行加工的 漸開線齒輪(Involute Gear) 特徵,其輪廓精確且符合微加工要求。
然而,對於常見的 鑽孔形狀(如圓孔),直接編寫 G-code 可能較為繁瑣,尤其當加工需求涉及多個孔洞時;因此,AGV5D 提供了一系列 預設鑽孔功能(Pre-Canned Drilling Functions),可透過 參數化程式碼(Parametric Code Blocks) 來簡化操作,減少手動編寫程式的時間與錯誤率;這些 預設函數 可用於加工 圓形、方形及圓角矩形 等幾何特徵,使用者只需輸入對應的參數,如孔徑、深度與加工順序,即可快速產生標準化的鑽孔軌跡,確保加工精度與一致性。
下列為 AGV5D 兩種 預設鑽孔功能(Pre-Canned Drilling Functions) 的範例,這些加工結果展現出近乎 垂直的側壁,且孔洞的 頂部與底部尺寸誤差不超過 1 微米,確保高精度加工;圖 4 顯示了透過 預設圓形鑽孔函數(Pre-Canned Circular Drilling Function) 產生的 圓孔陣列,其技術規格如下:
- 孔型:圓孔(Circular Holes)
- 側壁:垂直(無錐度)
- 孔徑:100 μm
- 基板材質:320 μm 厚的 氮化矽(Silicon Nitride)
此技術確保鑽孔過程的 精度與一致性,同時提升加工效率,使其適用於高密度微結構的製造需求。
圖 5 顯示了透過 預設方形鑽孔函數(Pre-Canned Square Drilling Function) 產生的方孔陣列,其技術規格如下:
- 孔型:方孔
- 側壁:垂直(無錐度)
- 孔徑:100 μm
- 基板材質:320 μm 厚的氮化矽(Silicon Nitride)
函數調用與參數設置
在 Aeroscript 程式中,函數的參數可以是固定數值,或是來自其他函數計算的變數,讓使用者能夠靈活調整加工設定;下方程式碼範例展示了一個 單向疊加圓柱鑽孔(Unidirectional Stacked Cylinder Drilling) 操作的函數,其中定義的參數控制了雷射的加工方式。
這些參數的設定方式與 CNC 加工中心 的鑽孔程式標準設定相似,使得雷射加工的控制更加精確,包括:
- 主軸轉速(Spindle Speed):調整雷射掃描的速度,以確保最佳的能量分佈與加工效率。
- 進給率(Feed Rate):控制雷射光點在工件上的移動速度,影響加工速度與材料去除率。
- 切削深度(Depth of Cut):設定雷射穿透材料的深度,以確保符合加工精度與材料移除需求。
這種 參數化設計 提供了 高度靈活性,允許使用者根據 不同材料特性與加工需求 進行 精確調整,確保 最佳的加工品質與效率。
位置同步輸出(PSO)技術
AGV5D 還運用了 位置同步輸出(PSO) 技術,實現基於距離的雷射觸發與能量控制,PSO 是一種強大的控制功能,它允許系統根據運動系統中每個獨立軸的位置回饋來定義雷射觸發條件,確保加工的精確性;透過 MHz 級別的編碼器回饋(Encoder Feedback),系統能夠在特定軌跡位置精準觸發雷射脈衝,確保雷射光點之間的間距保持一致,避免因速度或加速度變化而導致的觸發誤差。
由於雷射觸發是基於移動距離而非固定頻率或速度,使用者可以根據微加工需求,精確控制每個加工點的能量輸出(Fluence),以達成更精確的加工效果;圖 6 為一個 300 μm 直徑的螺旋加工範例,其中雷射光點間距為 6 μm,並透過 PSO 技術 確保雷射觸發間距均勻,即使在不同的速度與加速度條件下,雷射點仍能保持等距排列,確保加工品質。
強大的數據可視化與加工優化工具
Automation1 不僅僅是一款程式設計軟體,它是一個完整的自動化控制平台,具備數據可視化(Data Visualization)和加工參數調整(Process Tuning)功能,這些功能在伺服運動控制系統中至關重要,可提升加工精度與效率。
使用者可以在虛擬控制器上先行優化加工參數,然後將最佳化結果應用於實際硬體系統,這種模擬與實測結合的方式,使範例系統能夠提供深入分析(如 圖 7 所示),讓使用者監測並分析運動指令與雷射觸發狀態,確保加工過程符合預期。
範例系統的數據可視化與加工過程評估
範例系統使用 Automation1 提供的 1D、2D 和 3D 數據可視化功能,讓使用者能夠即時監測位置誤差,以評估加工過程的準確性與穩定性;此工具允許使用者繪製關鍵變數,例如:雷射光點的位置指令與五個自由度(DOF)下的實際位置誤差,使加工過程的控制更加精確。
在雷射加工開發過程中,使用者可以檢測運動軌跡是否產生較大位置誤差,這可能會直接影響加工品質;此外,該工具還能繪製雷射觸發訊號沿加工路徑的變化,以評估光點的放置精度,確保雷射能量在預定位置均勻分佈;透過這套完整的數據分析與監控工具,使用者無需實際切割零件,即可優化加工過程,提高製造精度並減少試錯成本。
加工速度
加工任何特徵所需的時間會受到多種因素影響,包括:雷射類型、雷射加工參數、材料性質、零件公差 及 運動性能,舉例來說,圖 4 所示的 100 μm 直徑孔 在 320 μm 厚的氮化矽(Silicon Nitride) 上進行 10 次加工,總耗時不到 1 秒。
AGV5D 針對 100 μm 孔 的 最高擺動(Trepanning)頻率 可達 800 Hz,確保高效能的微加工能力;然而,值得注意的是,任何伺服控制系統的動態限制(Dynamic Limits) 都取決於所執行的幾何形狀,不同形狀可能影響加工穩定性與精度。
Automation1 控制平台的 數據可視化功能 允許使用者在保持適當零件公差的前提下,優化運動軌跡與加工速度,確保加工品質與生產效率的平衡。
功率評級與熱穩定性
在開發 高功率脈衝雷射 的加工過程時,理解雷射能量對 AGV5D 內部 光學元件 的影響至關重要;AGV5D 的 光學系統 可承受的 最大功率 為 400 μJ,適用於 1030-1064 nm 及 515-530 nm 波長範圍內的雷射;這一能量範圍與許多雷射微加工應用相匹配,使 AGV5D 能夠充分發揮其 高動態運動設計(High Dynamic Motion Design),從而提升加工效率並提高產量。
由於維持熱穩定性同樣重要,AGV5D 採用了無內部控制器與驅動電子元件的掃描頭設計,此設計可最小化熱傳導,有效避免因內部電子元件產生的熱漂移(Thermal Drift),確保加工精度穩定;此外,所有馬達均採用水冷技術(Water Cooling),確保長時間運行時的溫度穩定,減少熱累積對加工精度的影響。
為了進一步提高耐用性與穩定性,掃描頭還配備 正壓氣流防塵(Positive Air Purge),可有效減少灰塵進入系統,降低光學元件污染風險;此外,系統還透過氣體冷卻(Gas-Fed Cooling) 直接冷卻鏡片與光學組件,以維持最佳光學性能。
這些標準功能顯著提高了加工的長期重複性以及機器間的再現性,確保生產過程的穩定性與零件品質的一致性。
應用範例:雷射微銑削(Laser Micro-Milling)
在 Z 軸高度固定不變 的條件下,透過 進給速率 控制 X 和 Y 軸 的移動,可以實現穩定的切削深度,確保加工精度與一致性。
單層銑削函數(Single-Layer Mill Function) 提供 參數化設定,允許使用者調整 切削直徑 和 擺動速度,以控制材料的去除率,並適應不同的加工需求;該函數可透過 簡單的 G-code 命令 啟動或關閉,並支援參數化定義,例如:切削寬度、切削速度、停留時間(Dwell Time) 等皆可透過變數設定,確保靈活性與可調整性;這樣的設計讓使用者可以根據需求,輕鬆定義粗加工(Roughing)和精加工(Finishing) 的加工路徑,提升製造效率。
圖 8 展示了一個 單層銑削操作的範例,其最終結果如下:
- 銑削寬度:200 μm
- 每次切削深度:10 μm
- 材料厚度:100 μm 不鏽鋼片
- 進給速率:3 mm/s
經過 10 次加工,即可完全切穿 100 μm 厚的不鏽鋼片,最終形成 垂直側壁(Vertical Sidewalls),並確保進出口尺寸的公差在 1 μm 以內,確保加工精度與穩定性。
靈活的銑削功能與深度控制
由於 銑削函數 具備高度靈活性,即使改變 單層銑削 的直徑,對切削深度的影響也極小;例如,當直徑從 200 μm 減少至 35 μm 時,切削深度仍保持一致,這是因為 擺動(Trepanning)操作的雷射速度 保持不變;此外,透過 PSO(位置同步輸出)技術,雷射光點的間距重疊度保持一致,確保加工精度;圖 9 展示了 35 μm 特徵 的 完整切削深度,其 頂部與底部尺寸公差不超過 1 μm,且適用於 1 mm 寬的加工圖案。
總結
五軸雷射進動掃描技術 在 雷射微加工 中扮演關鍵角色,使得 高縱橫比特徵(High Aspect Ratio Features) 能夠精準加工,形成垂直側壁,這對於各種高精度應用至關重要;這項技術的進步,讓 複雜幾何結構 與 嚴苛公差的零件得以高效生產,滿足對 極高精度與細節控制 有嚴格要求的產業需求。
技術應用領域
此技術適用於多種精密製造領域,包括:
- 醫療器材製造:
用於生產 心血管植入物(Cardiovascular Implants) 及 精密機械注射針管(Machined Hypodermic Tubing),確保醫療器材的高精度與生物相容性。 - 微電子加工:
應用於 探針卡(Probe Cards) 及 高密度互連(HDI) 基板與 印刷電路板(PCB)的 微導通孔(Micro Vias) 製造,提升電子元件的可靠性與導通精度。 - 汽車零件製造:
用於精密製造 燃油噴射器噴嘴(Fuel Injector Nozzles) 等關鍵零件,確保其耐用性與燃油效率。
➥ 了解更多 Aerotech 客製化運動平台 >
➥ 了解更多 Aerotech 特定製程運動控制平台 >
➥ 了解更多 Aerotech 雷射加工與自動化系統 >
AGV5D 的獨特優勢
AGV5D 系統 在 設計架構與程式方法 上展現獨特性,能夠顯著降低 加工過程中的熱漂移(Thermal Drift),這對於長時間加工精度的維持至關重要。
此外,AGV5D 與 G-code 編程的相容性 使其能夠與市面上的 CAM(電腦輔助製造)軟體 無縫整合,進一步縮小 傳統 CNC 加工 與 雷射微加工 之間的技術差距,這種高度整合的特性,不僅提升了系統的靈活性,也讓熟悉 CNC 加工的產業 能夠順利轉換至高精度雷射製造技術,成為解決精密製造挑戰的重要技術方案。
Aerotech 台灣合作夥伴:奧創系統 (UltronTek)
奧創系統 (UltronTek) 是 Aerotech 在台灣的合作夥伴,專注於提供高精度運動控制與測試解決方案,憑藉深厚的射頻 (RF) 技術專業知識與豐富的影像應用經驗,奧創系統能夠為客戶提供即時且靈活的技術支援,確保設備的高效運作與最佳性能。
➥ 了解更多 Aerotech 客製化運動平台 >
➥ 了解更多 Aerotech 特定製程運動控制平台 >
➥ 了解更多 Aerotech 雷射加工與自動化系統 >
此外,奧創系統 (UltronTek) 提供完整的客製化服務,我們的專業團隊將與客戶密切合作,針對不同應用場景提供量身打造的解決方案,確保系統穩定性與測試精度,提升生產效率與市場競爭力。
憑藉在地化的技術支援與全球領先的運動控制技術,奧創系統 (UltronTek) 不僅能快速響應客戶需求,還能確保產品與服務符合國際標準,為台灣產業提供最先進的自動化與精密運動控制解決方案。
關於作者
Bryan Germann 為 Aerotech 的產品經理,專注於 雷射加工產品,涵蓋 AGV 系列雷射掃描頭 及其相關的 Automation1 驅動與軟體控制功能;他在 高精度運動控制 和 自動化機械設計 領域擁有豐富經驗,並親自參與 高精度機械與自動化產品 的設計與生產管理,確保技術創新與應用的落實;Germann 於南卡羅來納大學獲得 機械工程學士與碩士學位,並擁有 17 項美國及國際專利,在精密製造與自動化技術領域具備深厚的專業背景。